Welding Digest
Jump to:
Articles prior to January 2023 can be accessed via our Publication Archive
News and Updates
Five Welders Celebrating National Welding Month
In honor of National Welding Month this April, we highlight five welders celebrating their role in the industry.
see moreEnsuring Overmatching Strength in Pipeline Girth Welds
A fundamental rule of welding engineering is that, in general, the strength of a weld should be greater than the strength of the base materials being joined. This is sometimes taken to mean that the strength of the weld should be greater than the specified minimum strength of the base materials being joined.
see moreESAB Donates $511,000 in Welding and Cutting Equipment To Agricultural Mechanics Student Contest at Houston Rodeo
Through its Future Fabricators program, ESAB has donated welding and cutting equipment with a retail value of $511,000 awarded today as part of the prize packages for winning competitors of the Agriculture Mechanics competition at the Houston Livestock Show and Rodeo, held at the NRG Center in Houston.
see moreThank a Robot for Helping U.S. Manufacturing
Robots have made our lives better. However, skeptics would have you believe that reshoring manufacturing and automation isn’t realistic. But the facts indicate the opposite.
see moreABB Opens Refitted, State-of-the-art U.S. Robotics Facility, Reaffirming Commitment to US Customers
ABB opened its refitted US robotics headquarters and manufacturing facility in Auburn Hills, Michigan, which will support ABB Robotics’ global leadership in developing and manufacturing cutting-edge robotic solutions in the US, for the US and the Americas.
see moreHypertherm Associates to Award Powermax Systems to 12 North American Schools as Part of Spark Something Great Grant Program
Hypertherm Associates, a U.S. based manufacturer of industrial cutting products and software, is now accepting applications for its Spark Something Great educational grant program.
see moreWhy Choose PTAW?
Plasma transferred arc welding (PTAW) hardfacing of components is a vital and complex science. Numerous military, industrial, and commercial products (e.g., pumps, augers, valves, etc.) depend on the hardfacing process to provide wear-resistant surface components.
see moreESAB Partners with EWI to Develop for ARC-DED Additive Manufacturing and SAW Processes
ESAB has donated systems for robotic and submerged arc welding (SAW) to EWI of Columbus, Ohio.
see moreSaving Money with Filler Metals
One of the easiest ways to improve productivity with filler metals is to use less of them, and to achieve that goal, all companies need to do is to follow the welding procedure specification (WPS) for weld size.
see moreFour New Cobots Are Showcasing a New Era of Automation
Created by Universal Robots (universal-robots.com), the UR30 is a compact, 30-kg (66-lb) payload collaborative robot (cobot). The cobot enables extraordinary lift. Its motion control ensures the perfect placement of large payloads.
see moreWhy Fabricators Continue to Choose Automated Arc Welding
Over the last three years, I’ve visited more than 40 different facilities, and one common denominator I’ve noticed is companies are moving toward welding automation or, at the very least, are considering investing in automated welding.
see moreWeld Setting Optimization for Collaborative Robots
Weld Setting Optimization for Collaborative Robots There are many videos showcasing how collaborative robots, or cobots as they’re commonly known, can weld. What is not always shown and less understood is how to maximize welding efficiency with cobots.
see moreRemote Manufacturing: Redefining the Skilled Workforce
Remote work is transforming the manufacturing industry and its skilled human workforce.
see moreThe Welding Advocate
Tiffany Orff is a multi-business owner and prison vocation teacher who shares the word about welding.
see moreForging Your Financial Future
For many welders who have embarked on a career that promises a bright future filled with opportunities and financial stability, making the right decisions when it comes to spending and saving money is important.
see moreStrengthening the Volunteer Experience and Board Governance
AWS president Michael Krupnicki speaks on the invaluable culture of the AWS community.
see moreWhat Drives the AWS Automotive Committees?
This Standards Action story brings attention to the AWS D8 Committee on Automotive Welding and its subcommittees. Keep on reading to find out more about their importance in the automotive industry and volunteering opportunities.
see moreWhat to Know about Aluminum GMAW Setup
Aluminum gas metal arc welding (GMAW) requires attention to detail and a base of knowledge to be successful. It’s also necessary to take precautions to avoid common mistakes.
see moreStrengthening the Volunteer Experience and Board Governance
AWS president Michael Krupnicki speaks on the invaluable culture of the AWS community.
see moreAWS Student Member Goes from the Family Farm to the Welding Classroom
Growing up in a small rural community in Economy, Ind., Jaron Baker was raised on his family farm that has been passed down from generation to generation for more than 150 years.
see moreWhat’s on the Horizon for AWS Standards
New technology and improved processes are enhancing these publications.
see moreAutomated Solutions for Bucket Welding Help Keep Manufacturers and the Earth Moving
Playing in the dirt has never been so high tech! A far cry from the metal Tonka trucks of our youth, today’s excavating equipment is massive and specialized from the electronics that power them to the buckets that scoop tons of earth in each fell swoop.
see moreLaser-Based Literature and Technologies Take Center Stage
Laser technology continues to adapt to the industry’s manufacturing needs. The literature is also refined for students and users, presenting new laser-based developments.
see moreHow ClearLight 2.0 Helmet Lens Technology Benefits Welders with Better Visibility
This welding helmet lens technology delivers more color and clarity before, during and after every weld
see moreRecognizing and Handling an Oxyfuel Torch Backfire
Learn the crucial steps to spot and safely shut down an oxyfuel torch backfire, ensuring a secure work environment.
see moreOptimizing Productivity with Grinding Wheels
Metal grinding is a demanding job. But it can be made easier by choosing the right product and the right tool for the specific application and using them properly.
see moreExamining the Flexibility of Additive Manufacturing
Changes driven by rapid innovation in 3D printing (3DP) technologies are afoot. Direct metal laser sintering (DMLS) has allowed an impressive list of metals to be built with additive manufacturing.
see moreChoosing PPE for Welding
Selecting the right safety equipment and garments is essential. This article discusses the critical factors when choosing personal protective equipment (PPE).
see moreWelding on the Farm
Welding on the farm has a long tradition, and sometimes it’s all that keeps things moving. But farm welding brings its own challenges. Sometimes repairs need to be made where power isn’t availa-ble. Farming equipment and machines aren’t all made from the same metal. And let’s face it, farms come with dirt and, well, more than dirt. Neither mix well with welding.
see moreStaying Safe When Using Abrasive Products
In a manufacturing environment, safety isn’t covered by a one-time seminar or meeting. Here are some tips for safe use of abrasive products and why safety is critical for the operator’s well-being and productivity.
see moreEnhance Welding Efficiency on Construction Jobsites
For construction contractors and steel erectors searching for ways to offset project slowdowns and labor challenges, paying attention to the following four tips on welding operations can help improve efficiency and performance on the jobsite.
see moreCobots Take Grinding from Good to Great
Cobots Take Grinding from Good to Great Professional welders know a good weld when they see one. They also know that there are some obvious reasons as to why good weld beads are ground once finished, such as better appearance, proper joint fit, or paint prep just to name a few. But great grinding takes time, precision, and a lot of hard work.
see moreA Comparison of Oxygen- vs. Air-Acetylene Torches
When it comes to brazing, there are two main equipment options to consider: oxygen-acetylene or air-acetylene torches. Traditionally, oxygen-acetylene setups have been dominant in many air-conditioning brazing applications across the United States. However, air-acetylene torches present a viable alternative. Contractors who have experimented with air-acetylene torches often appreciate their portability and lower operating costs, which can outweigh the slight trade-off of longer heating times.
see moreHow Poor Air Quality from Welding Fumes Harms Workers and Shop Productivity
Fumes generated during welding processes destroy air quality if not properly controlled. Dust collection systems need to be designed for the specific types of metals being welded and the regulations for permissible exposure limits and minimize hazards.
see moreAWS Sustaining Company Membership Solidifies Colorado Business’s Commitment to the Industry
AWS’s Sustaining Company membership is intended for forward-thinking organizations that want to promote an internal culture of continuous improvement and take an active role in shaping the industry.
see moreUsing Lean Principles to Improve Safety and Productivity in the Welding Shop
Adam Lawrence of Process Improvement Partners LLC, Lancaster, Pa., relates how by using lean business principles, he helped a welding shop cut its response time to major equipment issues from over two hours to under three minutes.
see moreThe Building Blocks to an Automated Robotic Welding System for Longer, Leaner Operations
The Building Blocks to an Automated Robotic Welding System for Longer, Leaner Operations Here’s how an automated welding system provider works with its customers to build these systems from the group up, thus mitigating risks and smoothening the transition to fully automated.
see moreKey Considerations for a Welding Fumes Extraction System
Every industrial manufacturing facility has unique processes. There’s no one-size-fits-all solution for managing welding fumes. This Q&A can help facility managers consider the most effective fume extraction strategy.
see moreSolving The Welder Shortage With Cobots
The skilled welder shortage is a global problem, but two companies overcame skepticism and embraced automation and robotics to bridge the gap between the number of welders needed and the number of available qualified welders.
see moreProper Robotic Welding Gun Configuration
The welding gun is a vital piece of equipment in a robotic welding system, serving as the conduit for the welding wire, gas, and power.
see moreFabricating the Enterprise’s Newest Successor
On August 27, 2022, Olympic gold medalist Katie Ledecky gave the command to Big Blue crane operator Charlie Holloway to lower the Enterprise (CVN 80) ceremonial keel unit into dry dock number 12 at Newport News Shipbuilding (NNS), Newport News, Va., a division of HII.
see moreTop Four Reasons to Use Arc Thermal Spray for Machine Components in Your Job Shop
Arc thermal spray, also known as twin wire arc spray, is one of the older and simpler forms of thermal spray coating. Thermal spray technology has come a long way, from spraying basic metals and simple alloys to, now, spraying extremely hard ceramics and carbides.
see moreAdditive Manufacturing in a Naval Aircraft Carrier Construction Project
Additive manufacturing technology, or 3D metal printing using layers of welds, enabled Newport News Shipbuilding to stay on schedule with construction of the nuclear-powered aircraft carrier Enterprise (CVN 80) for the U.S. Navy.
see moreImproving Communication between Generations
Each generation is different in important ways, but we can work to close the widening generational gap in the welding industry and revitalize the working relationships that are in critical need of repair.
see moreAdditive Manufacturing in a Naval Aircraft Carrier Construction Project
Additive manufacturing technology, or 3D metal printing using layers of welds, enabled Newport News Shipbuilding to stay on schedule with construction of the nuclear-powered aircraft carrier Enterprise (CVN 80) for the U.S. Navy.
see moreA Driving Force for Weld Quality
The AWS D8 Committee on Automotive Welding is responsible for the development of AWS standards on all aspects of welding in the automotive industry.
see moreHow Specifications Keep Aerospace Vehicles up to Standard
Regardless of how they're used, all aerospace vehicles are manufactured and repaired according to specifications. Manufacturers and tiered suppliers have stringent requirements that govern their processes to ensure components meet the end requirements.
see moreFixing the Labor Gap: Connection is Key
Leaders will need to rise above, offering mentorship that includes valuable interpersonal skills training, the ability to handle conflict, teamwork, listening, and more.
see moreHow to Make a Quality Shielded Metal Arc Weld
Welding student Mason Blaine performs a fillet weld on a T-joint while welding instructor Brian Wall watches his in-process bead placement. Pictures by Jodi Glass.
see more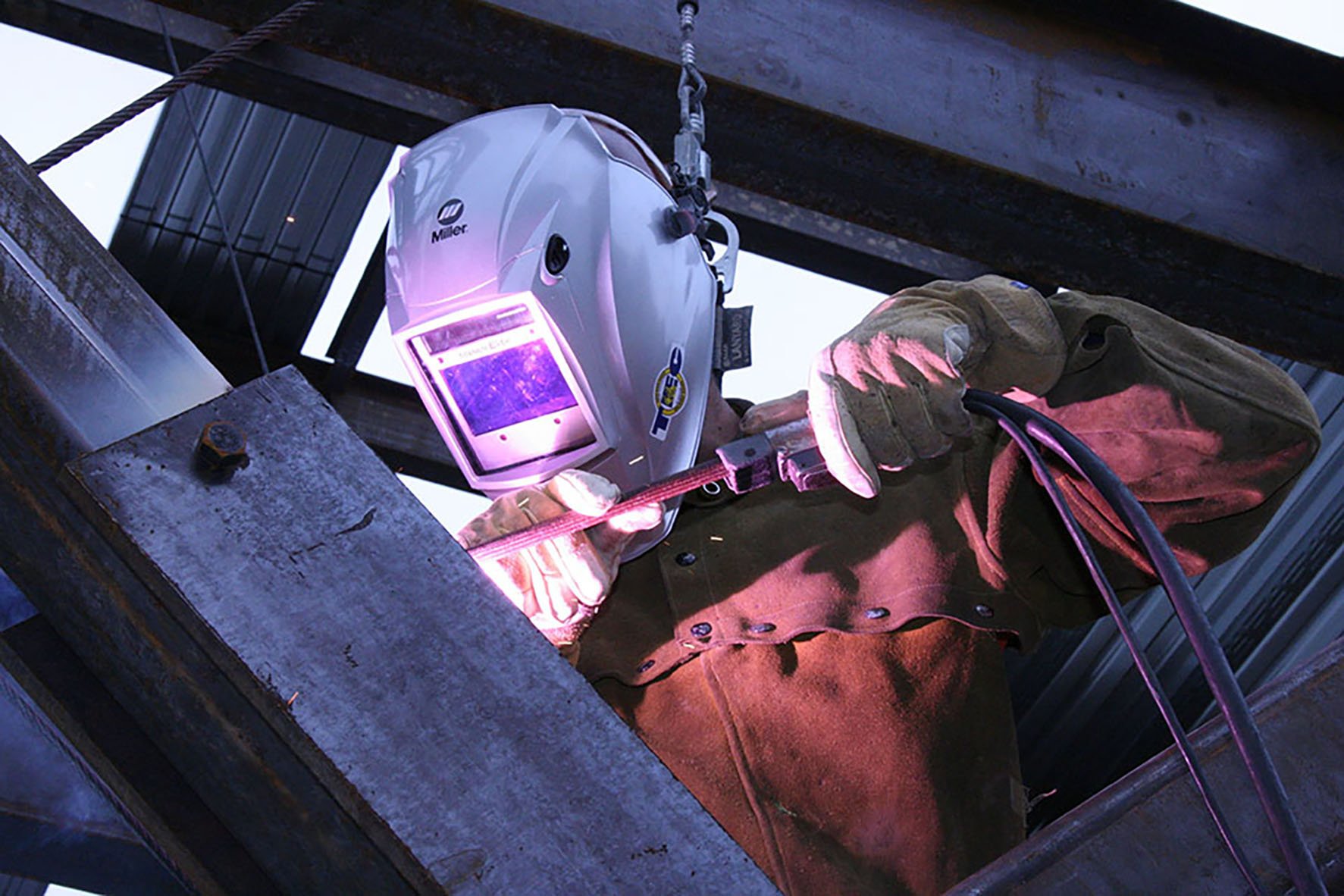
Enhance Welding Efficiency on Construction Jobsites
For construction contractors and steel erectors searching for ways to offset project slowdowns and labor challenges, paying attention to the following four tips on welding operations can help improve efficiency and performance on the jobsite.
see moreThe Education of a Welding Teacher: Tips from the Field
Throughout my nine years in the welding industry, I’ve had the opportunity to explore the world of teaching. I’ve learned a lot, and I’d like to share my experiences with you.
see moreBeyond the Arc: Welding Engineering Explained
“I have never heard of a welding engineer. What is a welding engineer?” That is a common response I have heard throughout my career.
see moreD20 Additive Manufacturing Technical Committee Makes a Call to Action
The AWS D20 Committee on Additive Manufacturing met at AWS Headquarters to discuss a new American national standard. D20 Chair Bill Mohr (middle, in a white shirt) leads the discussion.
see moreBuilding the New with Additive Manufacturing
Additive manufacturing (AM) of metals is a growing field that builds on the knowledge of metal and alloy welding behaviors. AM creates new material by fusing metal feedstock layer by layer using a computer-controlled heating plan.
see moreCWIs/SCWIs Can Get Certification Endorsement to Perform Welding Procedure Qualifications
The American Welding Society (AWS) proudly introduces the Welding Procedure Qualifier Endorsement, developed for existing Certified Welding Inspectors.
see moreReal-Time Data Tracking During Welding Operations
What if someone told you it is possible to capture welding data for each weld joint on a particular structure? You can see everything from amperage and voltage information to data that show specifications have been met.
see moreAWS Education: Welding Education for the Entire Career Arc
Welding is a dynamic industry with endless learning opportunities. And no matter where you are in your career, AWS Education offers comprehensive training resources that light the way toward your next goal.
see moreWelder Performance Qualification and Welder Certification
Misconceptions about welder certification terms and definitions are discussed.
see moreControlling a 7-Axis Robot for Continuous Internal Bore Welding
Gas tungsten arc welding (GTAW) is not commonly used in robotics because the process is erroneously believed to be too slow or complicated for robotics. But technological advances are changing that.
see moreHow Technical Committee Volunteers Help Develop AWS Codes and Standards
Standards are paramount to the infrastructure that makes up our modern civilization. And at the heart of these standards are technical committees, steering the propulsion for innovation through all the processes of the welding industry.
see moreHow to become a Standards Committee Member
AWS Standards Committees consist of over 1,800 volunteers, 200 committees, tasks groups, and 13 AWS staff. Together, they develop standards and other technical publications to serve the ever-changing welding industry
see moreAWS Standards: What They Are and how They're Developed
AWS is the leader in developing codes and standards that ensure consistency and quality across products, processes, and industries. But, what are Standards and Codes, and how are they developed?
see moreThe Benefits of Eddy Current Array Examination of Stress-Corrosion Cracking
Stress-corrosion cracking occurs when cracks link corrosion pits, causing multiple cracks in all orientations in the base material of pressure vessels, pipes, and storage tanks.
see moreStaying Safe during Resistance Welding
Resistance welding (RW) is a thermo-electric welding process in which the weld is made by a combination of pressure and current.
see moreComplementary Inspection Certifications
A discussion about additional certifications that enhance the CWI credential to broaden the inspection career.
see moreHarnessing the Teaching Power of Augmented Reality
Lewis and Clark Community College (L&C) in Godfrey, Ill., is using augmented technology to maximize learning, facilitate instruction, and reduce costs.
see moreLeveling Up Skilled Trades Education
While we often see virtual reality (VR) and augmented reality (AR) used for gaming, entertainment, and other commercial ventures, these technologies also have great potential for welder training.
see moreMaterial Conditions and Filler Metal Selection
When proper cleaning and part preparation of dirty or coated materials prior to welding isn’t possible, choosing the right filler metal for the base material conditions can help address quality issues and improve results.
see moreMultiaxis Laser Cutting in the Automotive Industry
Laser technology and the automotive industry have gone hand in hand for a very long time.
see moreCreating a Safe Environment While Gas Metal Arc Welding
You can make sure you are following the best preventative measures when working with the GMAW process by following the procedures outlined in this article.
see moreAn Introduction to SMAW and SAW Consumables
Quality shielded metal arc welding (SMAW) and submerged arc welding (SAW) welds typically start with using a quality consumable. For both of these commonly-used processes, choosing the right consumable for the application is key.
see moreThe Importance of Understanding AISC and AWS Codes
Following the requirements of codes and standards can save you significant dollars, create margin, and provide your firm with a quality reputation.
see moreChoosing the Right Welding Screen or Curtain
Many factors must be considered when choosing a semitransparent welding screen or curtain for protecting workers near the welding operation from harmful UV and blue light radiation.
see moreHow to Pass a Weld Test
In my journey as an instructor and inspector, I’ve monitored countless weld tests. More importantly, I’ve also taken many welding tests (known as welder performance qualification tests) during my career as a welder. These tests ranged from horizontal fillet welds to 6G ASME pipe tests. When the inspector certified my weld tests, I was qualified for production.
see morePublication Archive
View past issues of our magazines, including Welding Research Supplements in PDF format.